Internationellt team testar klimatförbättrat cement i Estland
I våras genomfördes ett fullskaligt försök med kalcinerad lera i en av Kunda Nordic Tsements cementugnar i Estland.
Kalcinerad lera är ett puzzolant material som kan användas för att ersätta en del av klinkern i cement. Tack vare lägre energiförbrukning och cirka 70 % lägre processutsläpp av koldioxid är kalcinerad lera ett lovande material som kan bidra till att minska cementets klimatbelastning.
Under de senaste sex månaderna har cementindustrin i Norden tagit viktiga initiativ för att minska koldioxidutsläppen genom lösningar med avskiljning och lagring av koldioxid. Att avskilja koldioxid vid anläggningen är avgörande för att avsevärt kunna minska klimatpåverkan från cement och slutligen få klimatneutral betong. Parallellt med detta behöver verksamheten arbeta med bränsleomställning genom att öka användningen av biomassa, med utveckling av cementprodukterna och med nya alternativa lösningar för råmaterial och den koldioxidintensiva klinkern. Förra året påbörjades ett projekt inom HeidelbergCement för att utvärdera möjligheten att använda kalcinerad lera för att ersätta en del av klinkern i cement. Det testades framgångsrikt under våren på Kundas cementfabrik i Estland.
Kalcinerad lera – utmaningar och fördelar
– Projektet har stor betydelse eftersom det bidrar till att kunna förverkliga HeidelbergCement Northern Europes produktstrategi som har starkt fokus på att minska koldioxidutsläppen. Att ersätta en del av klinkern i cement med puzzolana eller hydrauliska material är den bästa tillgängliga strategin för att minska CO2-utsläppen, säger Rolands Cepuritis, projektledare inom Development & Application vid Norcem som leder projektet med kalcinerad lera i Kunda.
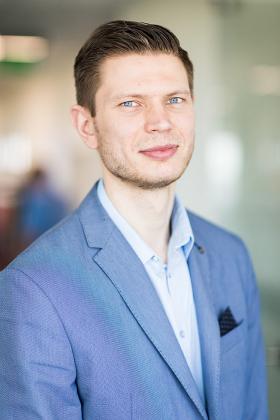
Kalcinerad lera är ett så kallat Supplementary Cementitious Material (SCM). Det är en beteckning som används för naturliga och tillverkade mineralmaterial som när de används tillsammans med cement bidrar till egenskaperna hos härdad betong genom hydraulisk och/eller pozzolanisk aktivitet. De vanligaste exemplen är flygaska, silikastoft och mald granulerad masugnsslagg. Men tillgången på konventionella SCM:er är begränsad vilket är en drivkraft för att finna nya källor.
– Kalcinerad lera av rätt kvalitet är en SCM som finns i tillräckliga mängder för att på ett hållbart sätt möta den faktiska efterfrågan. Leror av rätt kvalitet kan till och med vara ännu mer reaktiva än dagens mest använda SCM, flygaska, samtidigt som de är lika fördelaktiga när det gäller betongens beständighet, säger Rolands Cepuritis.
– En utmaning med kalcinerad lera är det större vattenbehovet jämfört med flygaska. Det kan dock hanteras genom optimering i produktionen och vid betongblandningen, förklarar han.
– En intressant aspekt är också färgen på den kalcinerade leran, som resulterar i rödaktig cement och betong. Det finns tekniska lösningar för att få en mer konventionell gråaktig färgton, men kanske kommer arkitekter och allmänheten att tycka om den rödaktiga betongen. Samtidigt kommer färgen på typisk betong bli annorlunda i framtiden, säger Rolands Cepuritis.
Han lyfter även fram hållbarhetsfördelarna med materialet:
– I en typisk cementblandning kombineras den kalcinerade leran med kalksten för att få en synergieffekt mellan de båda materialen. Under idealiska förhållanden kan man ersätta klinker med upp till 50 procent, medan 30 procent är ett mer förväntat resultat. Genom att använda kalcinerad lera kan vi minska cementens koldioxidavtryck med 7–8 procent jämfört med traditionell cement. Han understryker också att det är viktigt att leran har rätt kvalitet och det är här leran från Kunda kommer in i bilden.
Arvid Stjernberg, chef för Application & Development i HeidelbergCement Northern Europe förklarar:
– Efter en genomgång av möjliga källor hittade vi en lertäkt i Kunda i Estland som är intressant för framtida produktion. För att testa lerans egenskaper skickade vi under 2019 prover från täkten i Kunda till en liten testanläggning i Tyskland för semiindustriella provningar. Resultaten visade att leran i Kunda har bra potential och att nästa steg var att göra ett fullskaligt försök i Kunda-anläggningen.
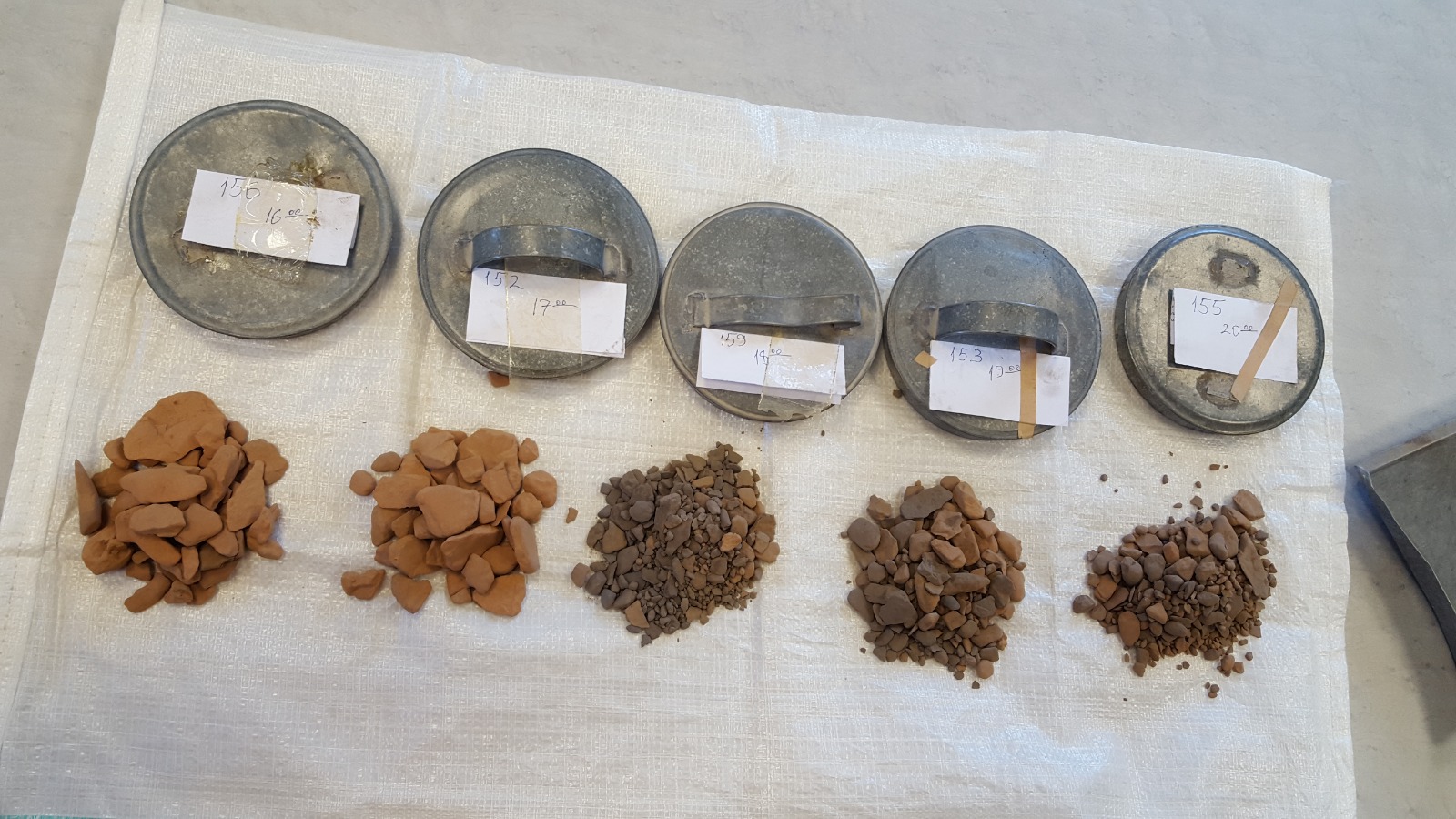
Smart planering
Förra året bildades ett internationellt projektteam, en koncernövergripande expertgrupp med sju olika nationaliteter. Teamet stöds av HeidelbergCement Technology Center (HTC) och HeidelbergCement Global Research & Development. För att lyckas med ett projekt i den här skalan krävs detaljerad planering.
– Först gjorde vi en projektbeskrivning och bestämde omfattning och målsättning. Nästa steg var att titta på den faktiska anläggningen i Kunda för att utvärdera de tekniska möjligheterna, processrisker vid provningarna, nödvändiga uppgraderingar av anläggningen samt att utarbeta flera möjliga fullskaliga försöksscenarier. Vi tog också fram en detaljerad budget för vart och ett av scenarierna och gjorde en offentlig finansieringsansökan för FoU, som senare godkändes. Därefter utarbetade vi detaljerade riktlinjer över provningarna och gjorde en kvalitetskontrollplan och en riskbedömning, förklarar Rolands Cepuritis. Det sista steget i projektet var själva genomförandet av försöken i Kunda, vilket visade sig vara en utmaning.
– Vi stötte på flera flaskhalsar, exempelvis omfattande regn som gjorde råleran mjuk och klibbig, vilket innebar att vi inte fick en stabil matning till ugnen. Själva ugnen hade inte varit i bruk på över ett år sedan klinkerproduktionen upphörde i Kunda. Försöket blev också en läroprocess för ugnsoperatörerna som var tvungna att gå över från klinkerproduktion till en helt annan typ av förbränning. Tack och lov lyckades vi lösa problemen inom rimlig tid genom ett systematiskt arbetssätt.
– Pandemin försvårade också det internationella teamets besök på plats vilket gjorde att det lokala teamet fick mindre externt stöd under försöken i maj 2021, säger Rolands Cepuritis.
Förutom honom själv bestod det externa teamet på plats av Nicolas Pato, Senior Engineer Industrial Tests & Implementation från HeidelbergCement Global R&D i Tyskland som ansvarade för kvalitet samt Marek Majchrowicz från Polen, Senior Process Manager Pyroprocess vid HTC.
– Vi fick ta fram en samling epidemiologiska säkerhetsregler som alla deltagare i studien var tvungna att följa. Att lyckas efterleva dessa regler var ytterligare en utmaning, men det var värt det eftersom projektteamet under de tre veckorna lyckades producera kalcinerad lera med god kvalitet, avslutar Rolands Cepuritis.
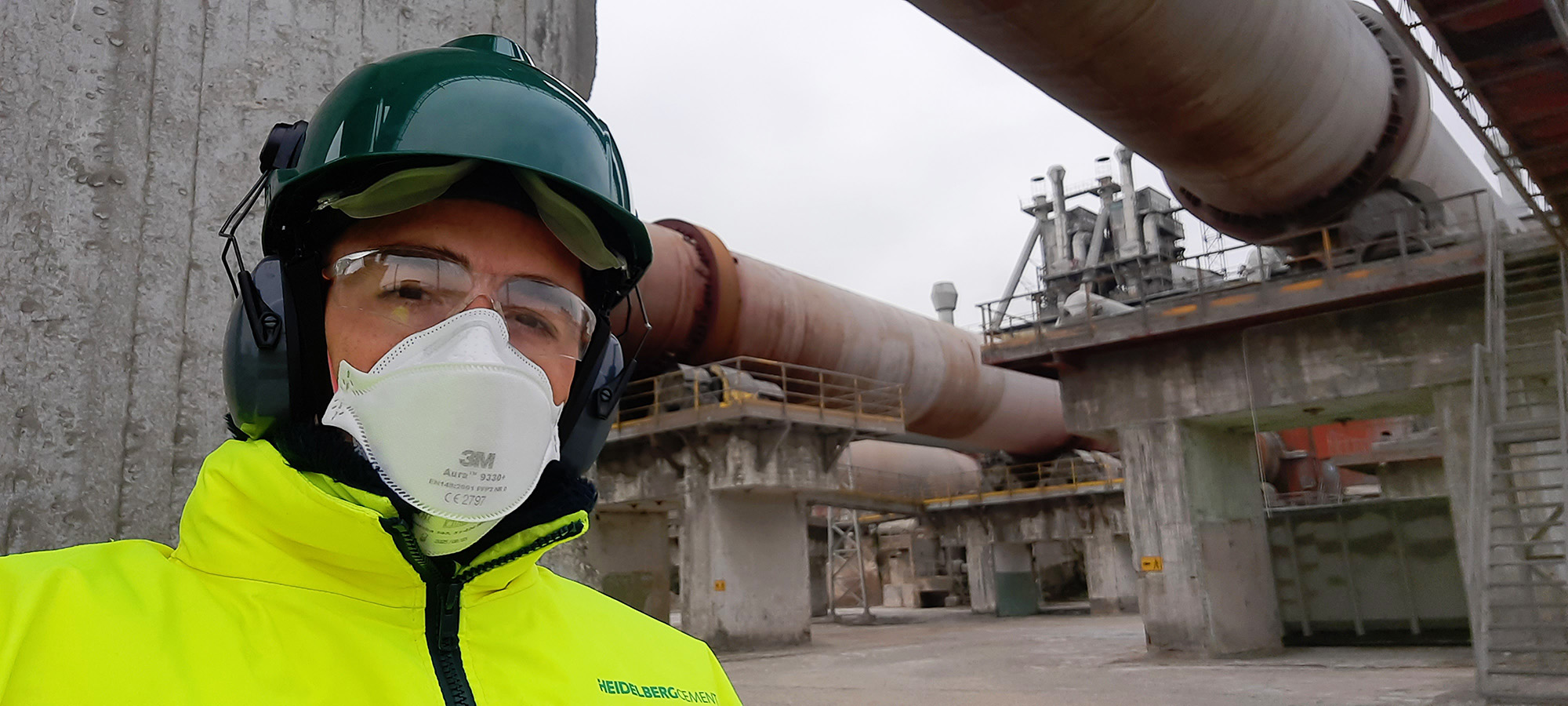
Nicolas Pato tillägger:
–Tack vare det stora engagemanget från laboratoriet i Kunda och med stöd från Global R&D fick vi fram välfungerande rutiner för att följa den kalcinerade lerans kvalitet under försökets gång.
Marek Majchrowicz är nöjd med resultatet:
– Med hjälp av vår erfarenhet och det goda internationella samarbetet lyckades vi uppnå våra mål med försöket. Vi klarade av en stabil matning av lera till ugnen och producerade 700 ton högkvalitativ kalcinerad lera. Han understryker att dessa kunskaper även kommer att användas i andra projekt som företaget överväger att starta, och inte enbart för den eventuella produktionen på Kunda-anläggningen.
Framtidsutsikter
Meelis Einstein, VD för Kunda Nordic Tsement och medlem i projektets styrgrupp är mycket nöjd med resultatet.– Det har varit roligt att driva det här projektet i Kunda – vi har ett fantastiskt team och kompetenta medarbetare som fick värdefulla erfarenheter genom försöket.
Lerprojektet i Kunda kommer att utvärderas från ett affärsmässigt perspektiv senare i år. I samband med det kommer det beslutas om produktionen av kalcinerad lera ska påbörjas i Kunda.
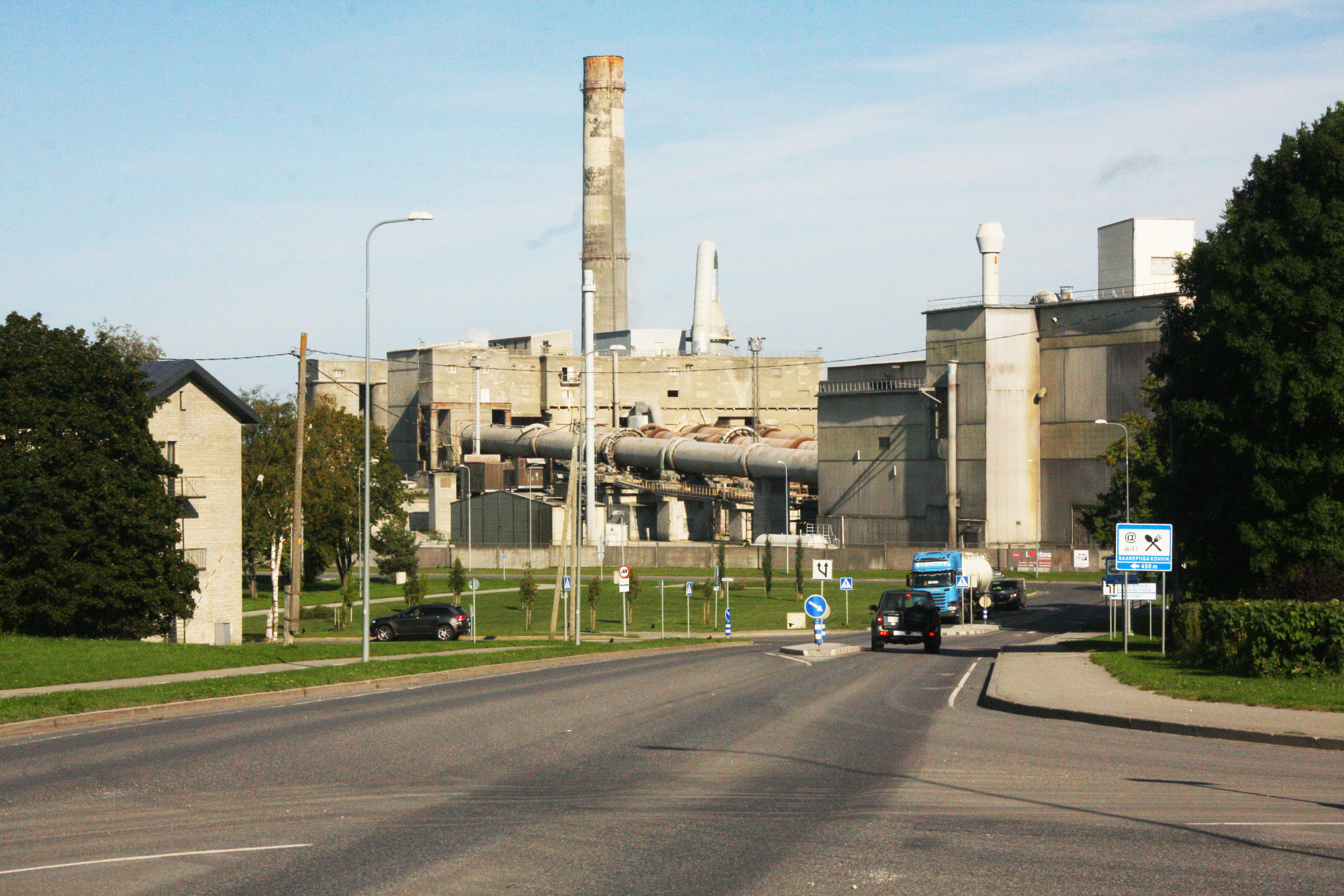
(Klinkerproduktionen stoppades i Kunda år 2020 på grund av den avsevärda kostnadsökningen för CO2-utsläpp, vilket hade stor inverkan på anläggningen som har höga utsläpp på grund av äldre produktionsteknik.)